A deacon from Italy ordered as a gift for his upcoming priestly ordination bei uns a very complex processional cross at the beginning of the year. The processional cross should be possible in its form and equipment a historical model (“Protestant Cross of the Cathedral Chapter”) from the Cathedral chapter of St. Paulus Cathedral in Munster from the 13th century without repeating all the details of the original too exactly.
The approx. 40 cm large processional cross was to be elaborately decorated with precious stones and stones on the front, based on the original Filigree be decorated and on the more modest back receive a small engraving with a representation of Mary from the original home parish of our customer.
Our proposal therefore included a type of furnishing that both appropriately quotes the Romanesque model and at the same time builds a bridge to modern times.
Pigeon-blood red rubies, large rock crystals as symbols for the stigmata of Christ and a sky-blue topaz as a symbol for God the Father were selected as precious stones for the four ends of the cross. Emeralds, sapphires and amethysts were chosen to decorate the inner surfaces of the cross as supports for the Corpus Christi.
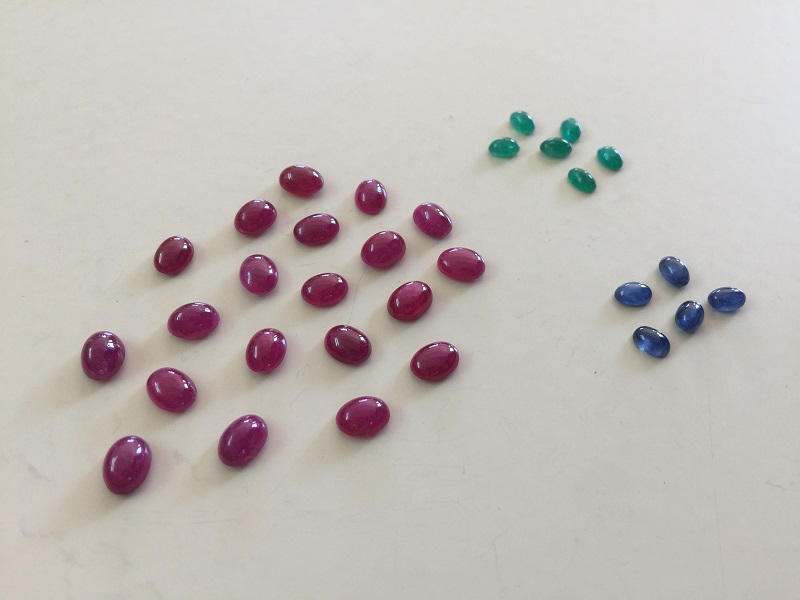
Furthermore, our customer wanted a case for safe storage of the cross as well as a carrying rod that could be divided as far as possible and a suitable stand. For this purpose, together with our case supplier, a concept for a practical storage and the most obvious removal order of the individual parts as well as for the precisely fitting cut-out of the case’s foam inserts was first created and then coordinated with the customer:
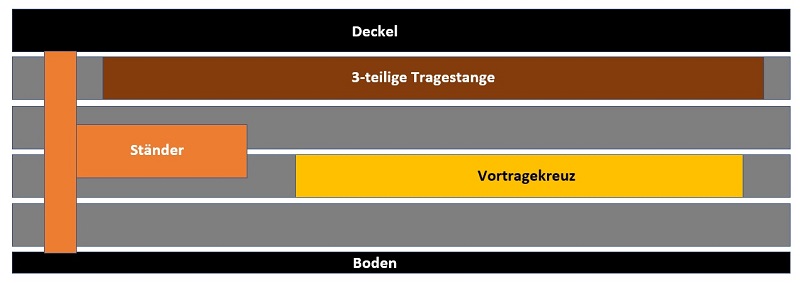
Then we ordered a perfectly matching carrying rod made of turned dark oak and divided it into three elements of the same size, which can later be easily and yet very stably screwed together again and, if necessary, can be conveniently stowed in the carrying case together with a cross and stand in the meantime.
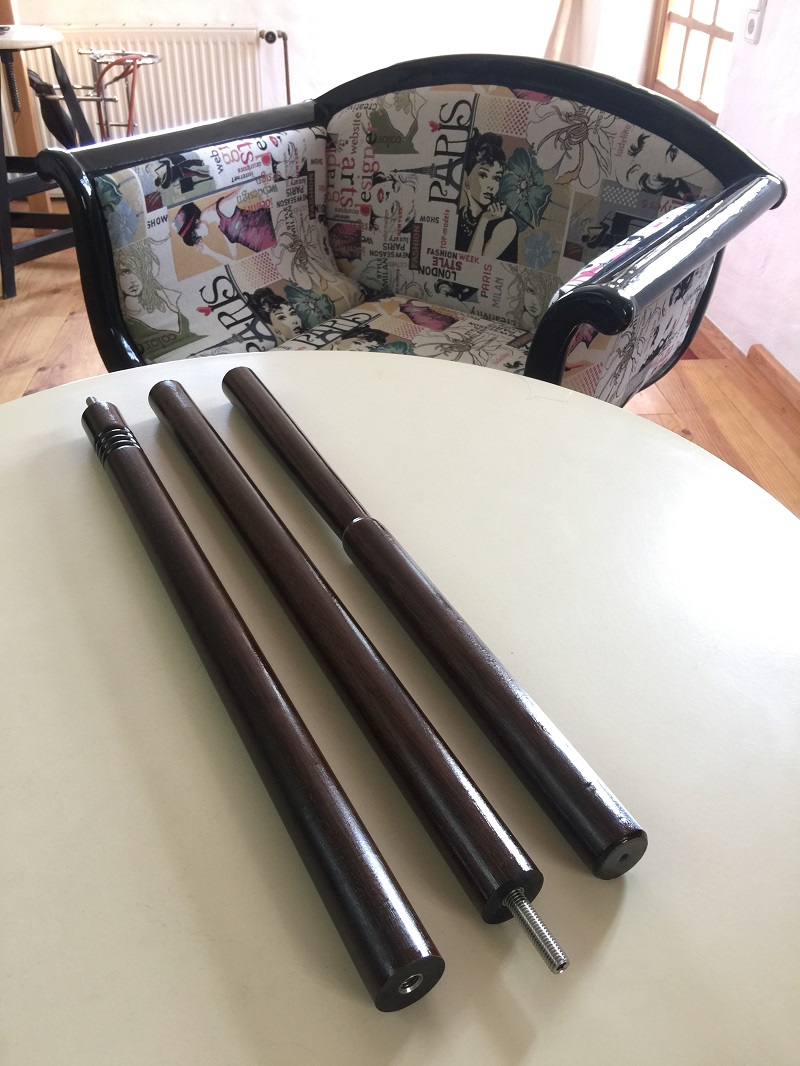
For the engraving of the only 5 x 5 cm large depiction of Mary on the back of the cross, we were able to win an experienced hand engraver from the Rhineland, who handcrafted the depiction desired by the customer (a large historical stained glass window from the church of his home parish) stylistically exact and in a remarkable quality as an engraving on the small gilded fitting.
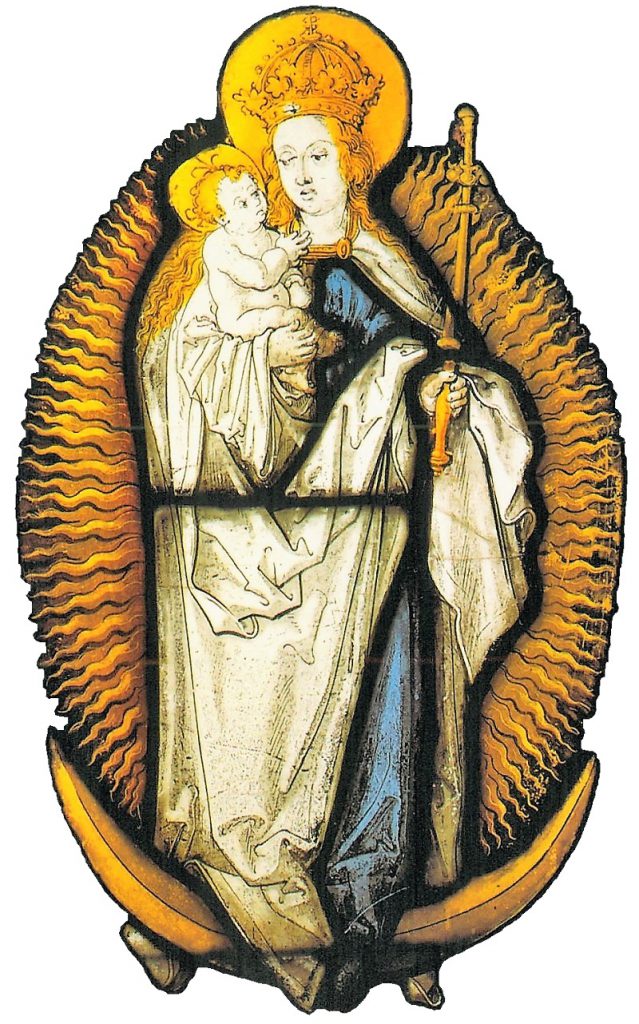
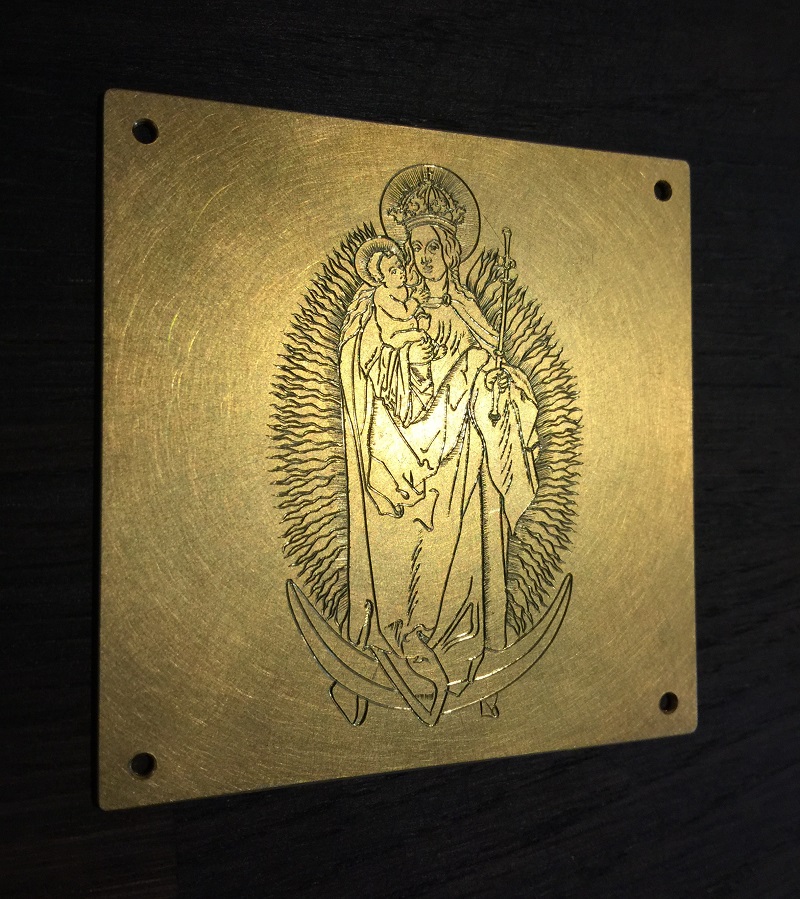
The lines are scratched or cut into the metal by hand with the help of so-called engraving burins of various thicknesses. Considering that such work does not tolerate a single mistake, it is easy to see the craftsmanship and amazing skill of the master in the finished engraving.
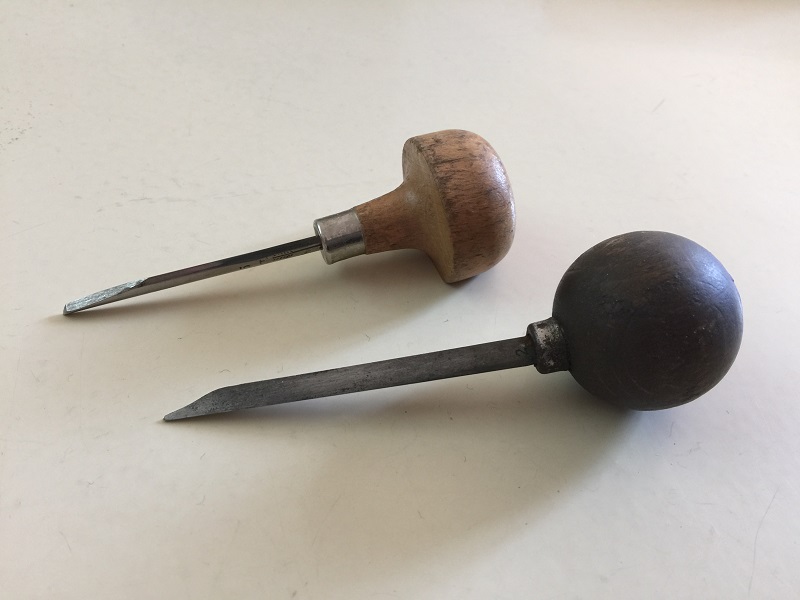
Next, we made the wooden core for later stable accommodation of the gold-plated decorative fittings and "married" it 😉 for the first time with the approximately man-high carrying rod.
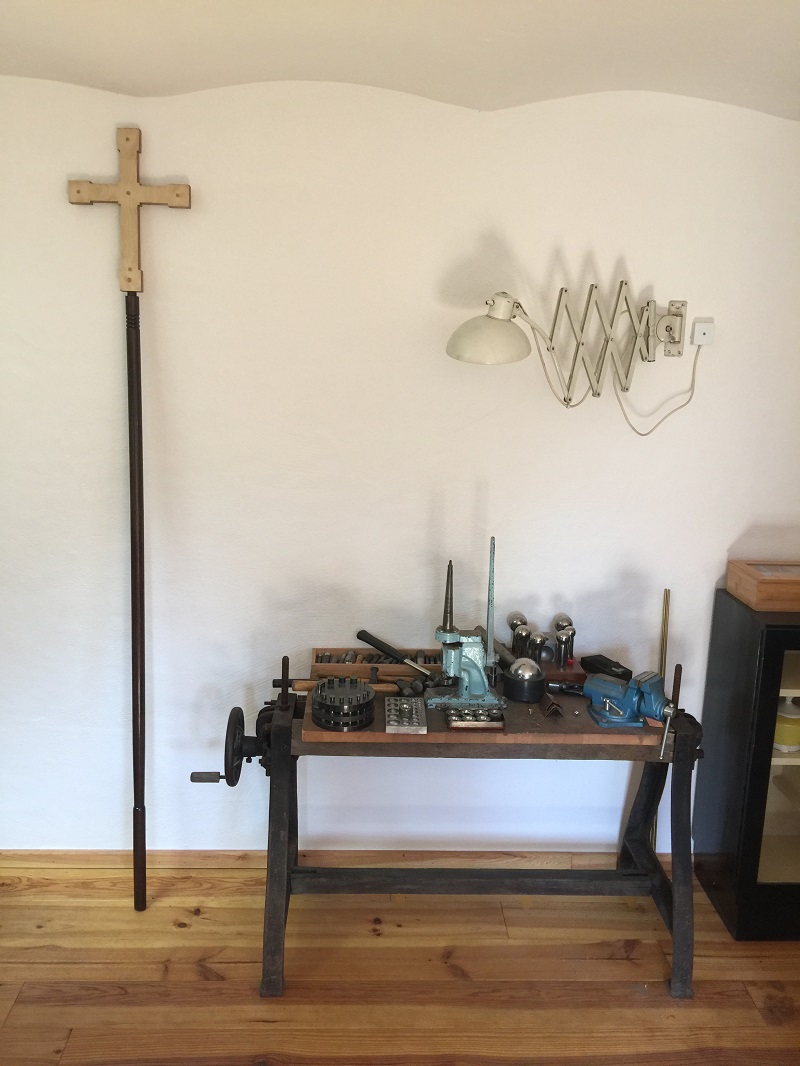
Now it was slowly getting to the finish line: The first handmade fittings were fitted with the settings for the gemstones that would later be provided there, so that the filigree jewelry could be adapted exactly to the gaps that were only now available.
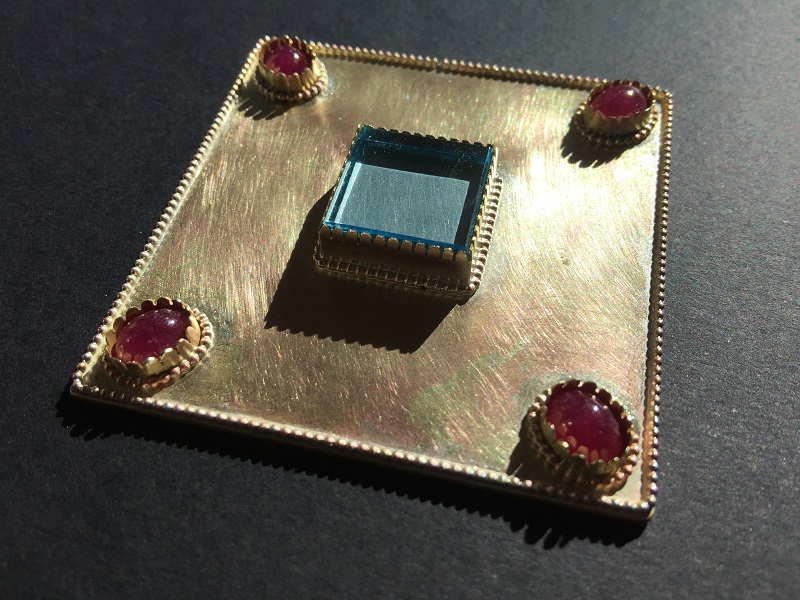
Now the way was finally "clear" for the premier class: the filigree. The subsequent filigree jewelery was coordinated with the customer using a prepared example. The form of the individual filigree ornaments was based almost exactly on the high medieval models from the 12th and 13th centuries.
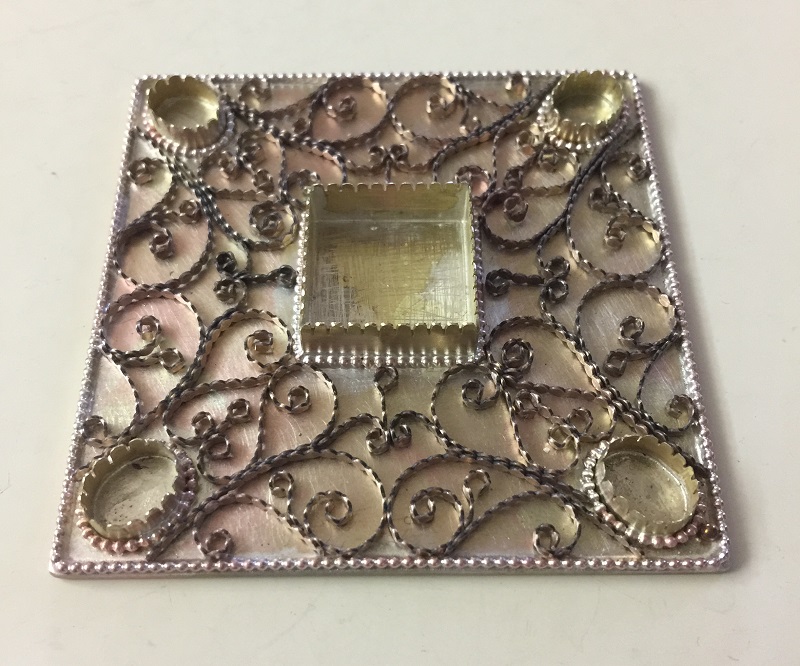
Now came what was perhaps the trickiest step: soldering the filigree. The individual filigree ornaments were soldered with silver hard solder. As you can see, the fine webbing made of the wafer-thin filigree loops has to withstand a lot: 😉
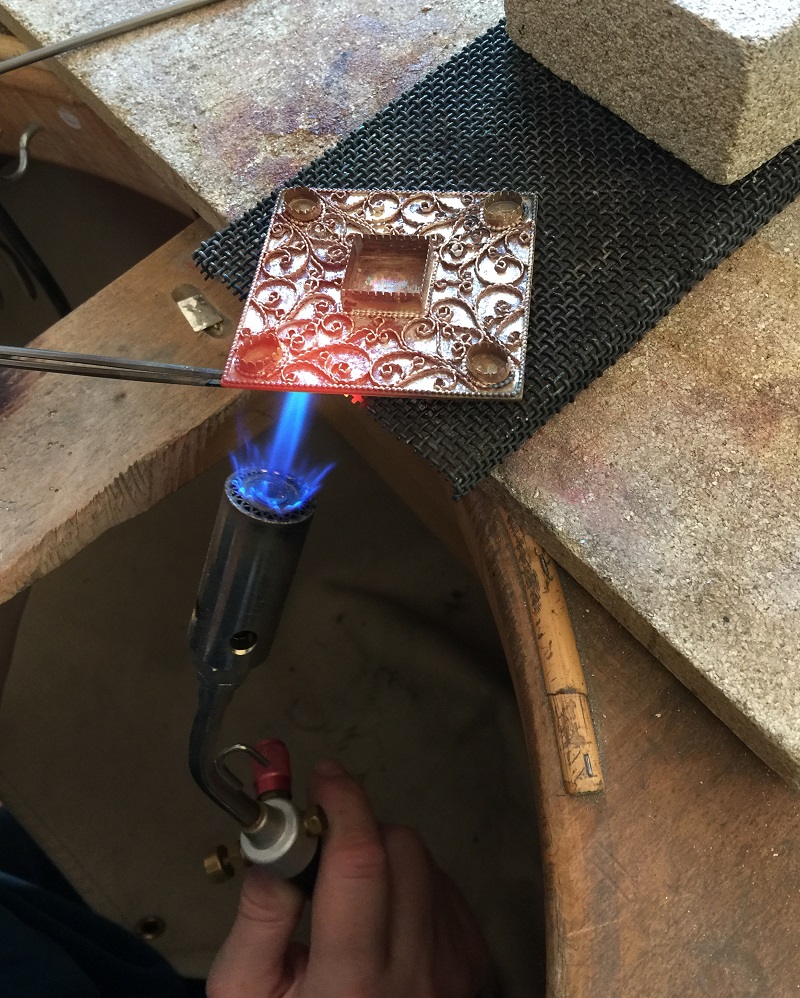
After the filigree fittings have finally come out of the fire, they still look a bit battered. It is now difficult to imagine what magical splendor the later gilded and partially polished fittings on the processional cross will unfold in the bright sunshine, for example.
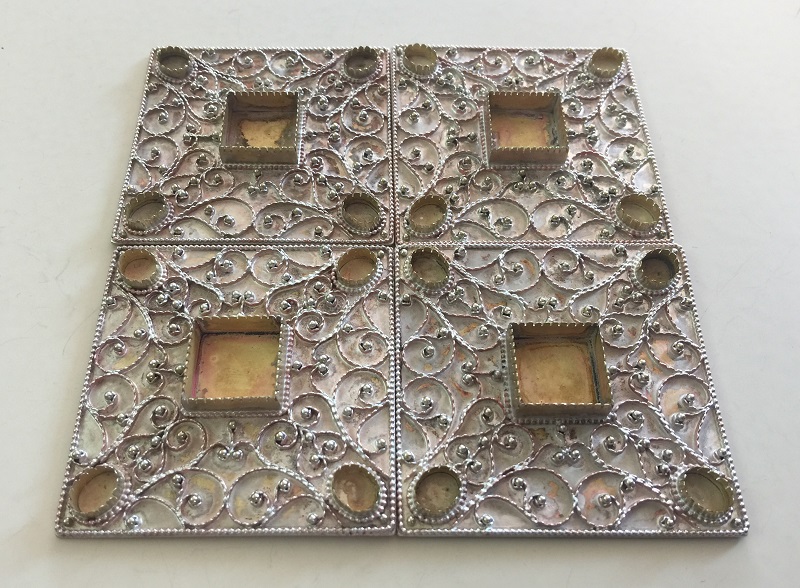
Now that the almost 200 decorative pins have also been individually polished, they can finally take their bath in the gold plating. The result almost looks like a work of art Gunther Uecker. 😉
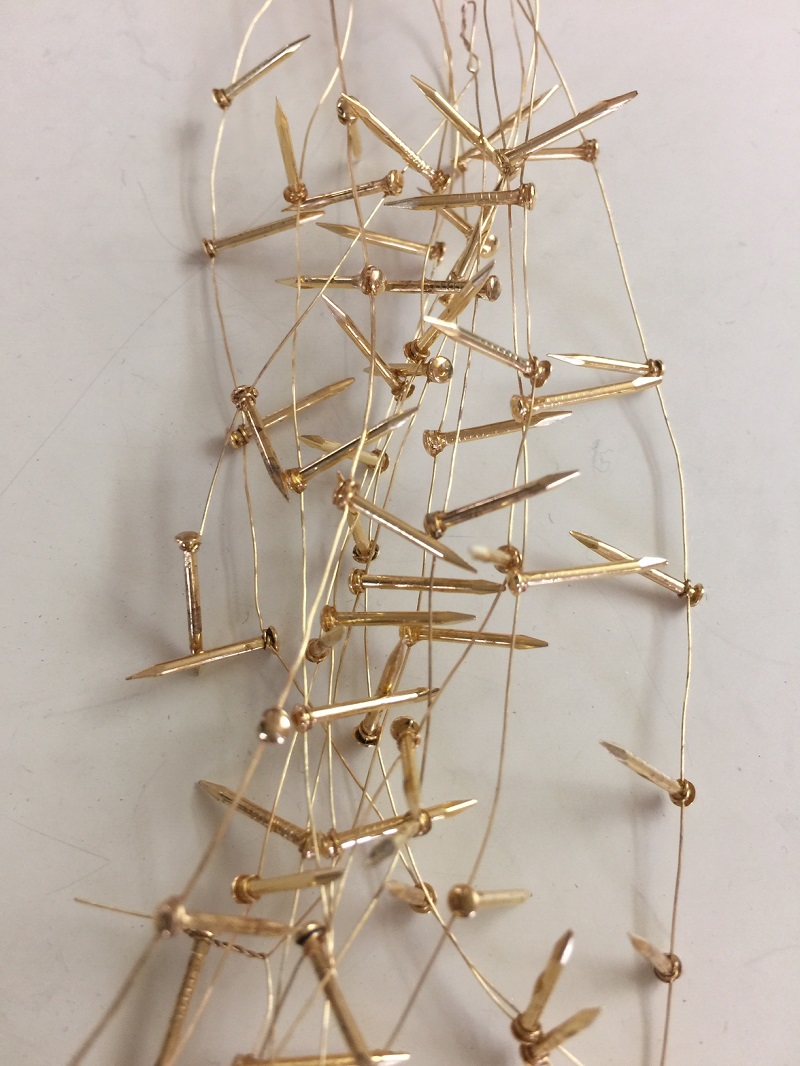
With the help of the new decorative nails, the freshly gilded side and back fittings as well as the hand engraving in the center of the back of the processional cross could now be mounted.
Here the contrast of the rather modern and simple back to the classic and much more elaborate front of the cross was particularly important to us.
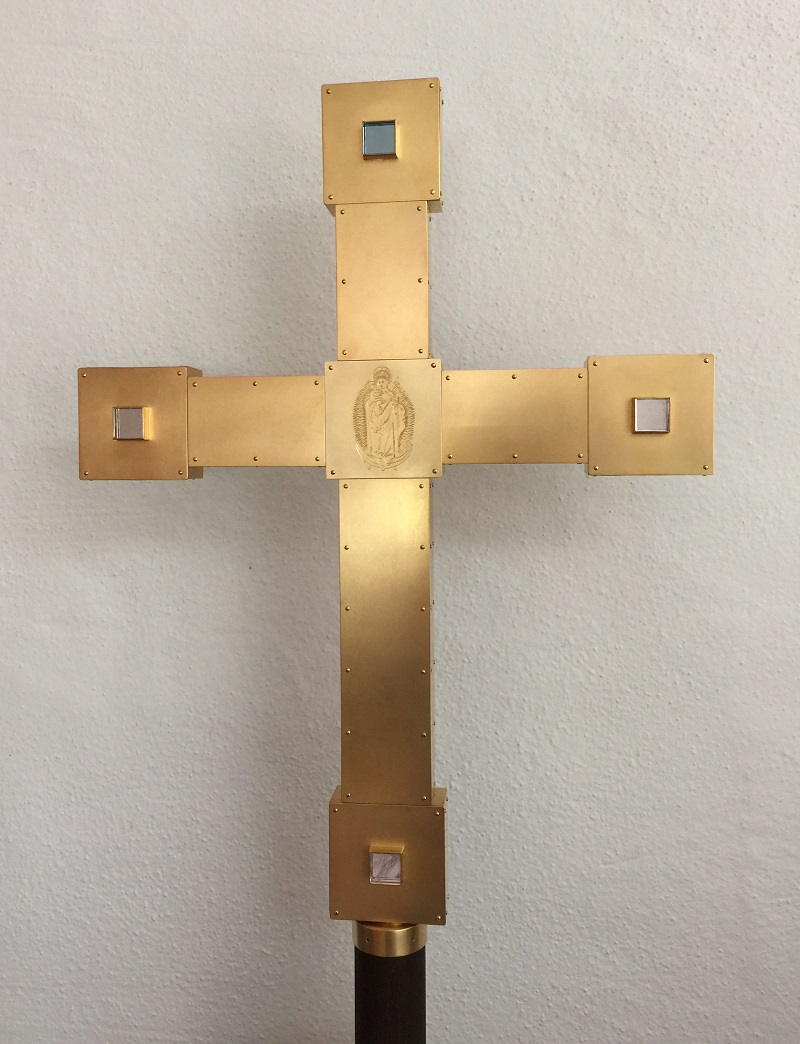
The filigree fittings on the front are finally gilded and could be tried on for the first time. The effect of the sophisticated techniques of the medieval master goldsmiths, who also worked with elaborate filigree jewelry made of pearl wire, is already slowly becoming apparent.
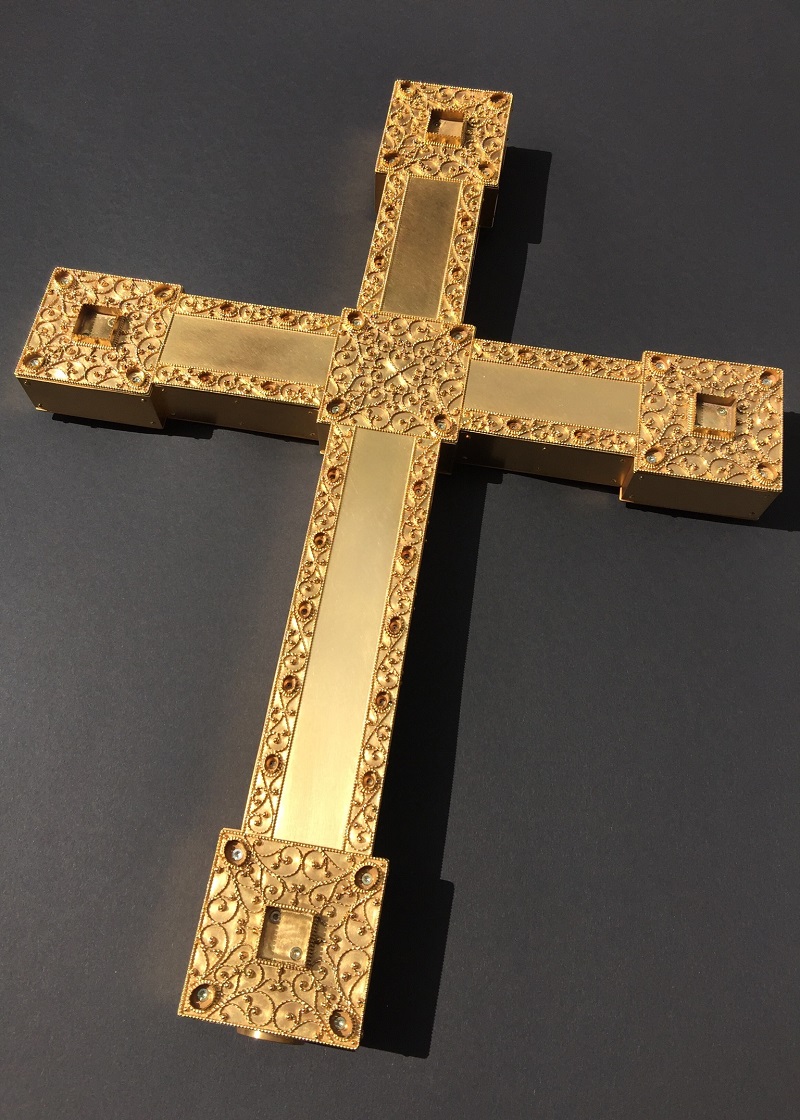
The effect of these medieval beaded wire ornaments is simply overwhelming. The many light reflections on these different surfaces glitter in the sunshine like a set of many small diamonds. Wonderful.
Before the gemstones were finally set, an individual underlay was selected for each gemstone, which emphasizes its special character and can compensate for minor differences in the cut height. This base consists of an extra rhodium-plated silver plate that has either been finely or rather roughly hatched or even completely polished to a high gloss.
Such underlays are always helpful when the gemstone is completely surrounded by its setting and therefore no more light can enter from below or from the side. Incidentally, the medieval goldsmiths also helped here, for example with a so-called “waffle foil”, which reflects the incident light from below through the gemstone and helps to show the gemstone in all its original beauty.
Now everyone could cabochons used and their versions finally closed. After that, the processional cross shone in all its glory for the first time and all the decorative ornaments merged into a homogeneous unit.

Last but not least, the Romanesque figure of Christ, specially cast in brass, had to be mounted. However, it was important to first remove the traces of the foundry - such as the very strong sprues - and to undo them optically. Some details - such as the hair and the crown of thorns - which were somewhat weakened by the casting, were reworked manually and thus largely adapted to the original template again.
After that, the Corpus Christi was also galvanized with fine gold and could then finally take its final place in the center of the front of the processional cross.
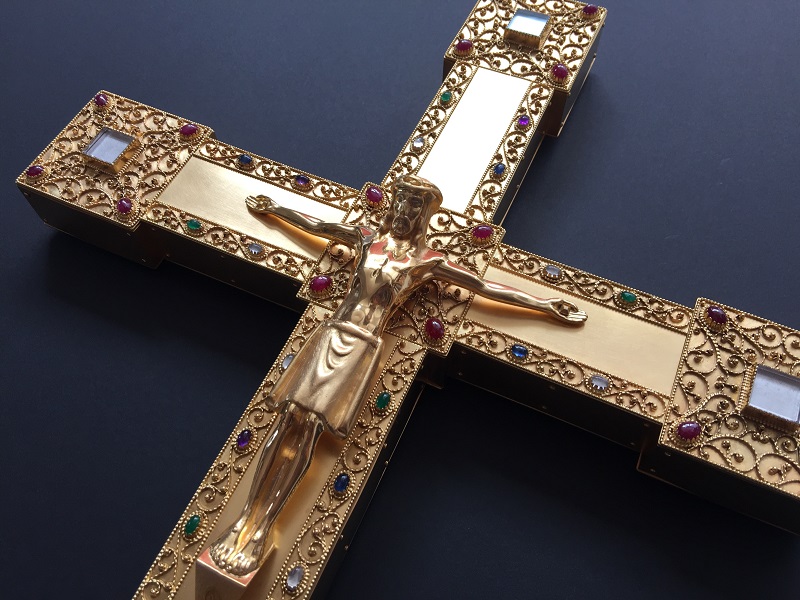
Made! Everything worked and all elements are in their intended place undamaged. The result was simply overwhelming, even for us. Seeing the finished cross, igniting an almost magical light and vivid glitter in the direct sunlight, was the greatest reward for this intricate work.
As a last action, the corresponding suitcase could now be packed. Before that, we gave the large and the small carrying rod a gold-plated decorative sleeve with small gold-plated decorative nails. These sleeves increase the valuable effect of the carrying rods that are screwed in later and form a worthy transition between the dark lacquered oak wood and our goldsmith work.
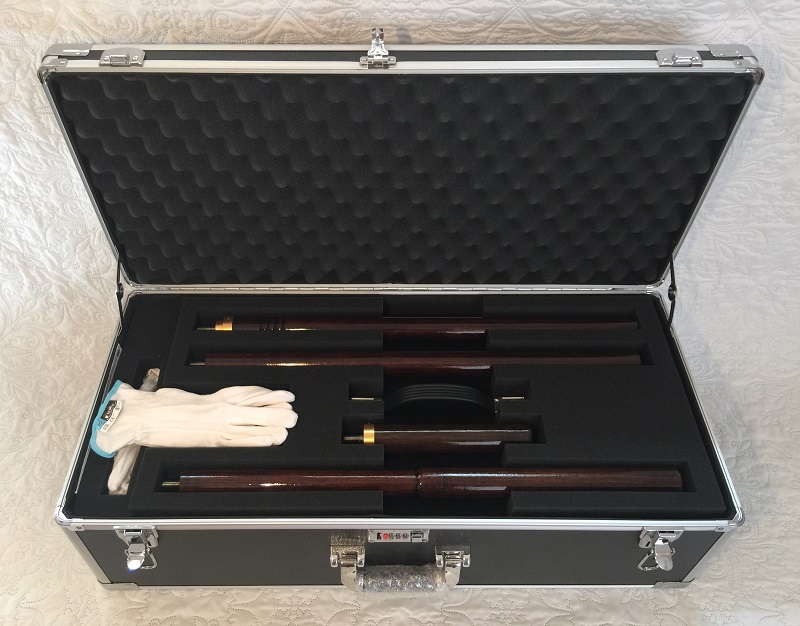
Finally, here are some “impressions” of our beautiful “Protestant Cross for Italy”:
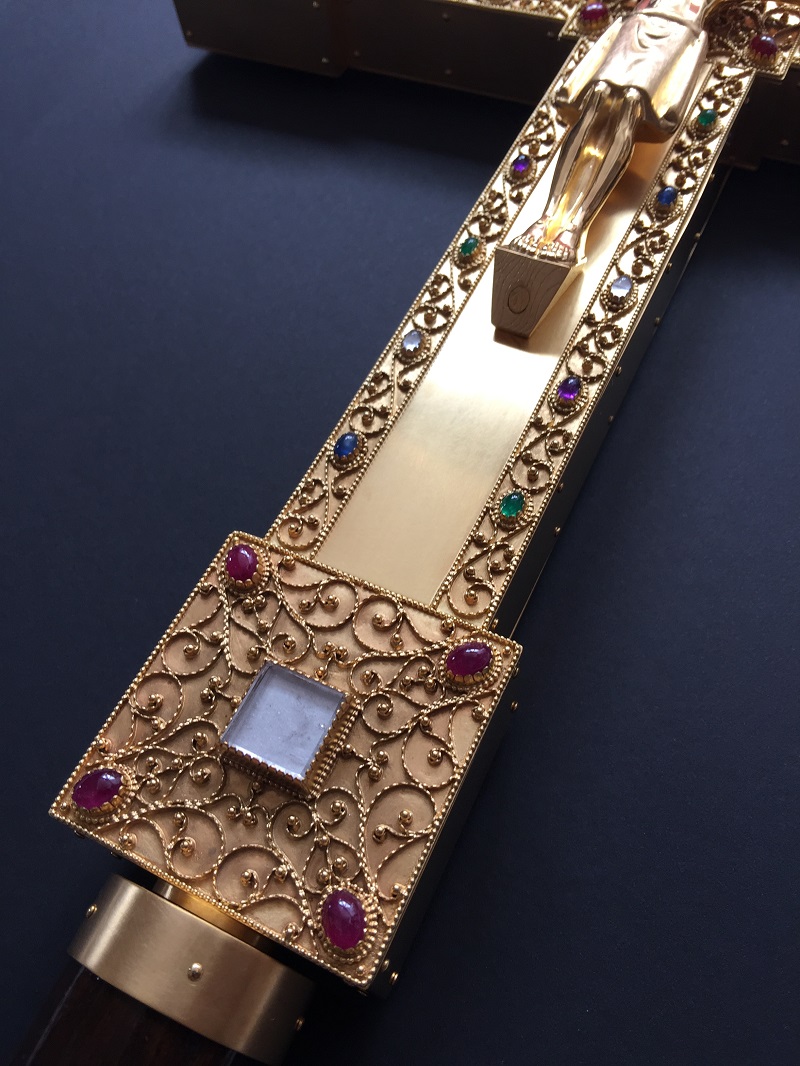
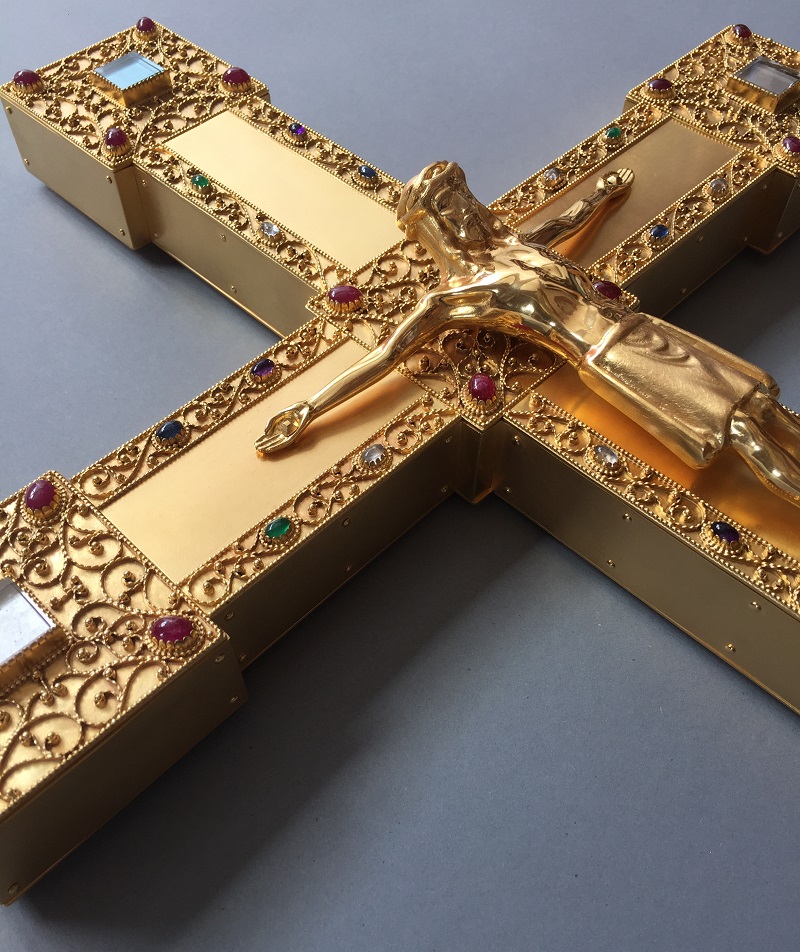
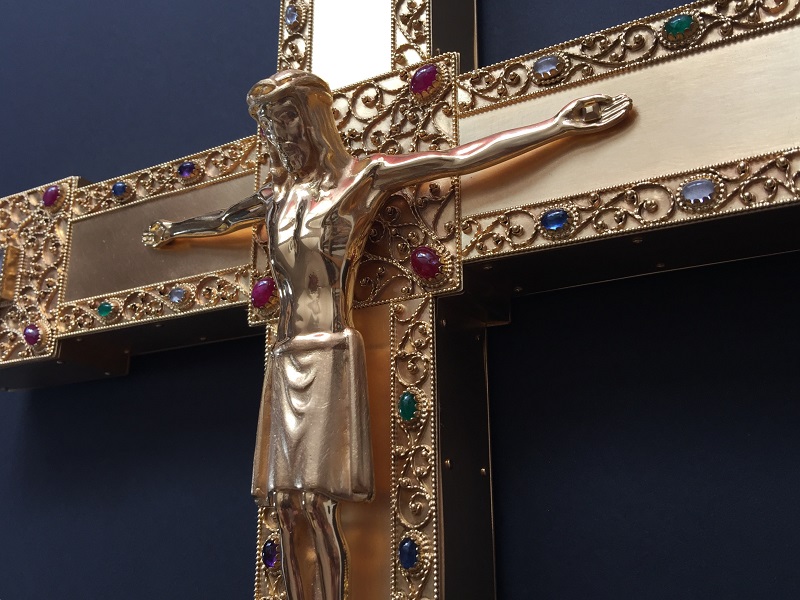
The final feedback from our customer shows us that we were apparently able to fully meet our customer's expectations, both in terms of quality and the type of processing:
“…I can't even put it into words how beautiful it turned out. I am simply speechless with great joy and enthusiasm and in awe of this beautiful work! A big compliment for what you have created here! So clean and meticulous... just gorgeous! I really thank you from the bottom of my heart for all your efforts and dedication! ... It was really a pleasure to work with you ...
... I'm really very grateful and happy to get to know such great and committed people who do their job with so much passion and joy. It was a pleasure to develop and realize this work with you. A dream is now coming true! I am sure that I will have great joy with this cross. But not only me, but also the many people who will see it at the services. All for the greater glory of God! God bless you for all your hard work...”
Father M., Italy