At the end of 2015, the LVR LandesMuseum Bonn surprised me with a whole series of very interesting orders.
For the exhibition planned for the following year “EVA'S BEAUTY CASE” some exhibits (replicas) should be regilded.
Furthermore, a replica of a Franconian almandine disc fibula should be made and its manufacturing process detailed and scientifically documented .
In addition, a showcase with a goldsmith's workplace and an educational film about the various production steps of the gold primer running on a monitor was planned.
The highlight, however, was the order to make a replica of a medieval precious stone brooch. This replica should be presented on a goldsmith's workbench together with extensive information and materials on the manufacturing process of the gold fibula.
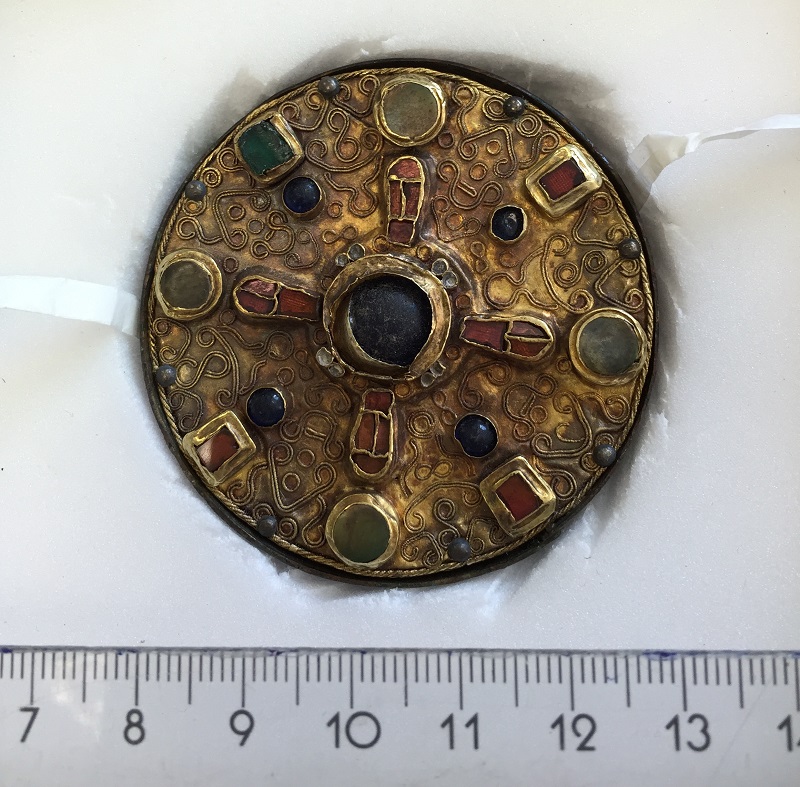
A total of three trades were involved in the manufacture of the replica: Harold Heinrich as a gem grinder, Angela Liane Wagner for the glass flow ornaments and I as a goldsmith for the production and "final assembly" of the fibula.
Work began in March 2016 on the basis of the original and the scientific material analyzes and their discussion with art historians from the LVR LandesMuseum Bonn.
First of all, the necessary amount of 730/- gold was alloyed in the same way as the material analyzes of the medieval original had shown: with shares of silver and copper. This roughly corresponds to the 750/- yellow gold that is common today.
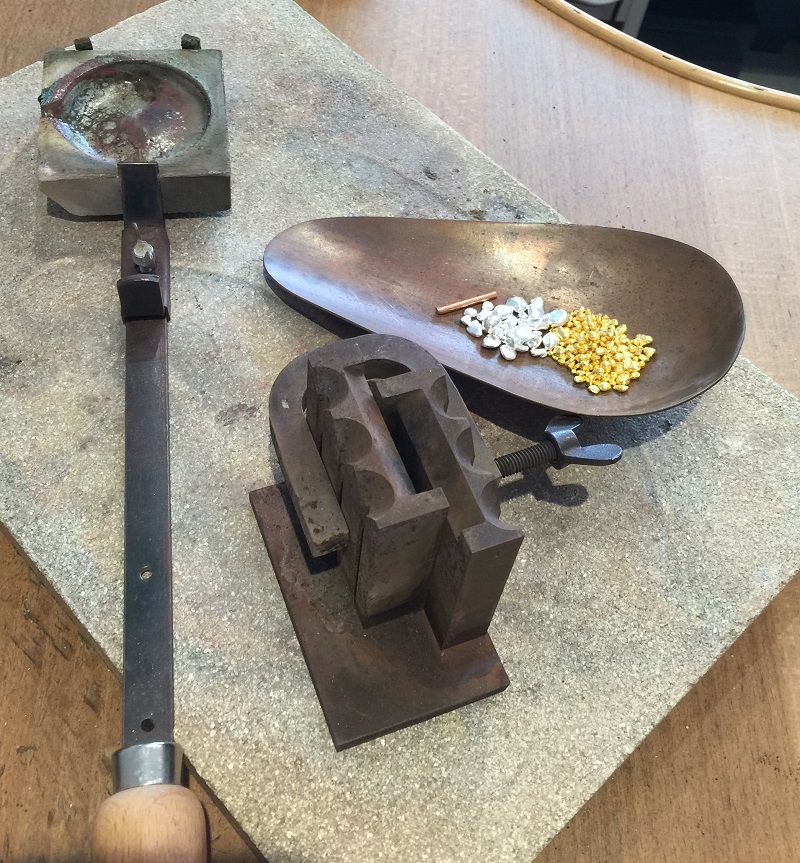
The show plate of the gold fibula and the individual settings for the gemstones were made with the alloy obtained in this way, which is true to the original.
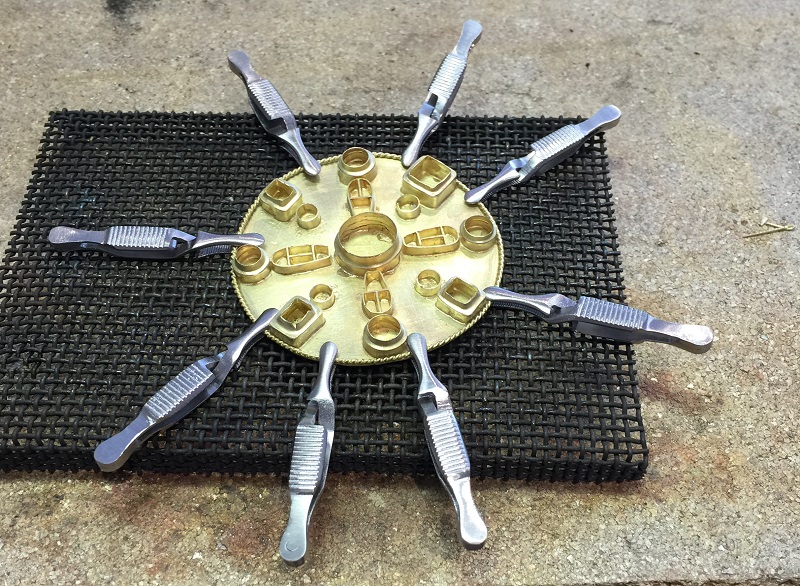
An extra grooved gold wire was used for the filigree ornaments, which is soldered onto the gold sheet. A so-called "waffle foil" was used as a base for the red almandine gemstones, which consists of 999,9 fine gold and which - as in the Middle Ages - makes the red gemstones shine particularly brightly.
After the specially cut gemstones and glass flux ornaments were finally delivered on time, I was able to start with the "final assembly" of the fibula and set all the stones. For this purpose, the fibula was embedded in special putty:
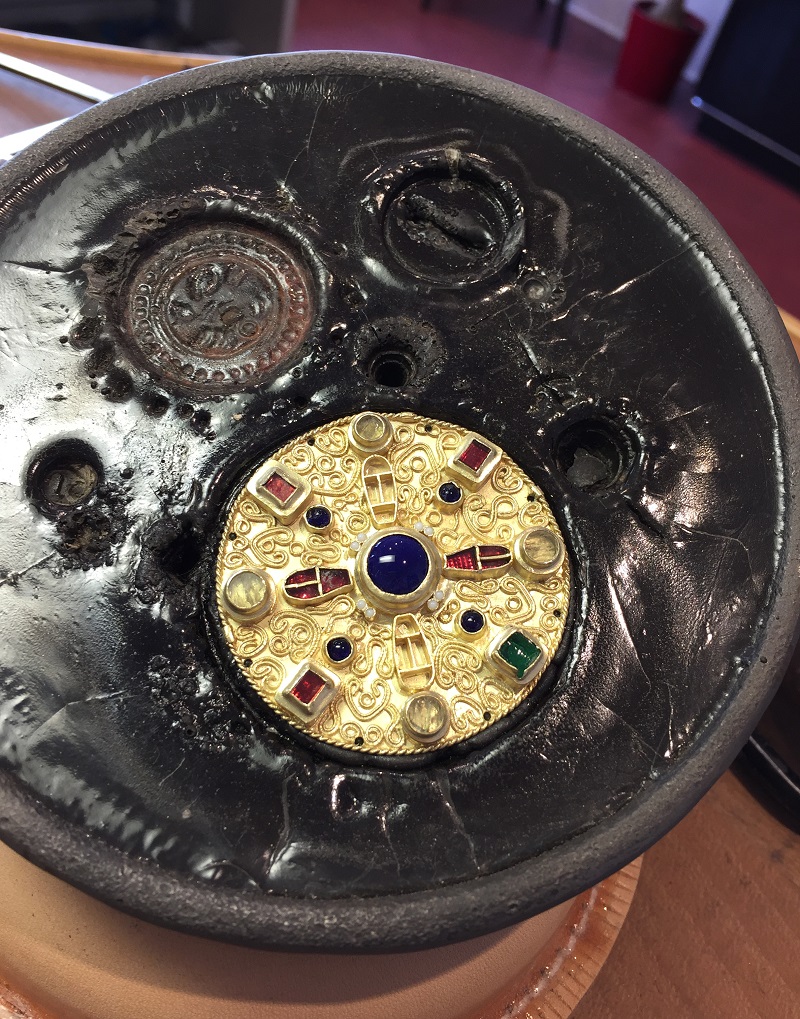
The finished gemstone gold brooch was finally presented together with a goldsmith's workplace and lots of additional information on the manufacturing process of the brooch in the "EVA's BEAUTY CASE" exhibition:
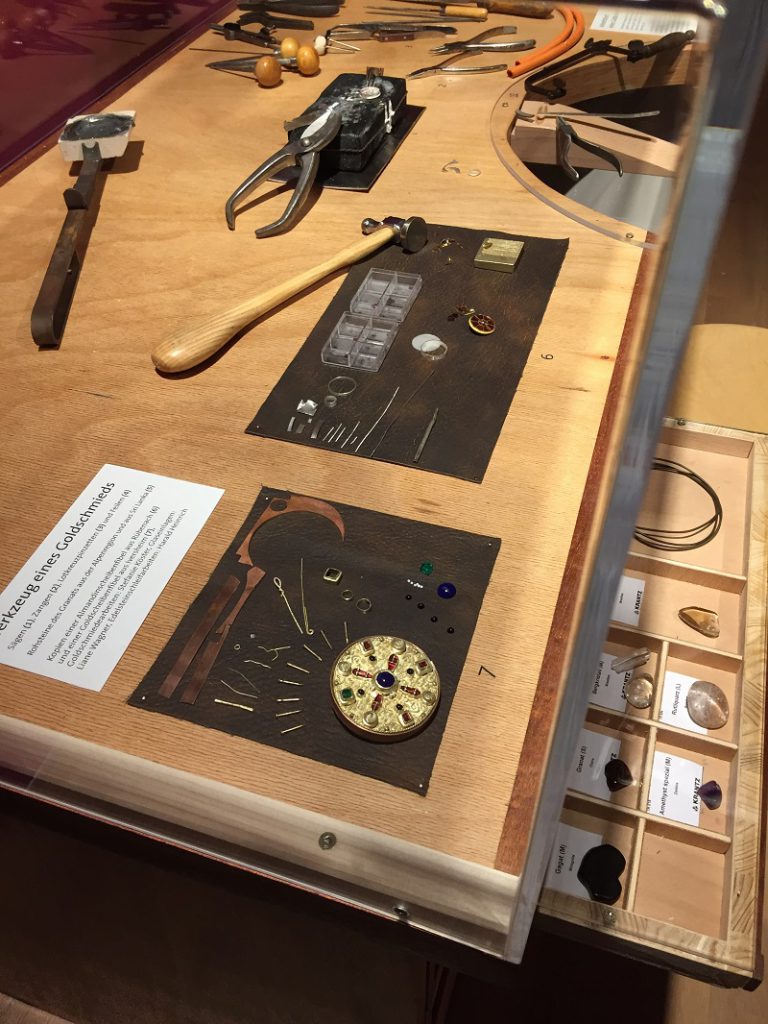
In any case, the icing on the cake for me was that a monitor above it showed photos of the entire manufacturing process and the craftsmen who carried out the work.
It's a very special feeling when you suddenly see your own picture on a museum monitor. 😉
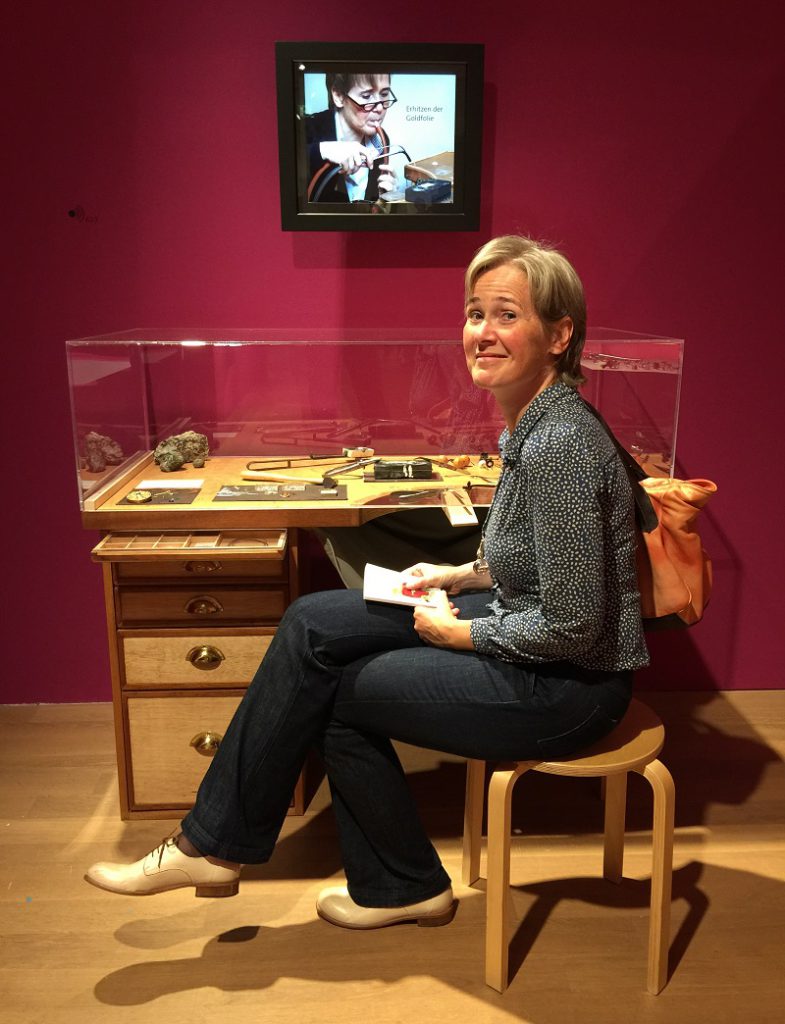